Smart Shipping: How Propeller Design, Hull Coating & Scrubbers Boost Energy Efficiency
- Davide Ramponi
- 7. Apr.
- 5 Min. Lesezeit
My name is Davide Ramponi, I’m 20 years old and currently training as a shipping agent in Hamburg. In my blog, I take you with me on my journey into the fascinating world of shipping. I share my experiences, my insights, and my progress as I work toward becoming an expert in the field of Sale and Purchase — the trade with ships.
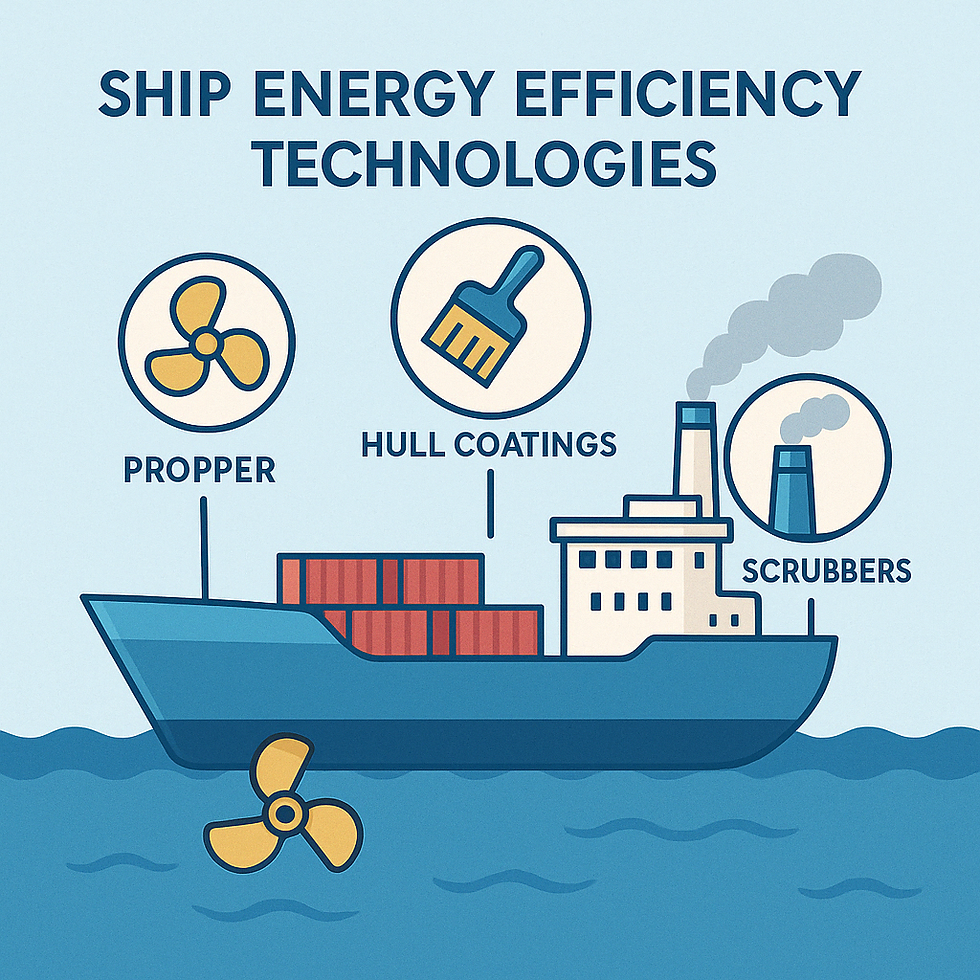
Energy efficiency has become one of the most urgent—and rewarding—focus areas in modern shipping. Whether you’re managing a fleet or preparing for your first vessel purchase, reducing fuel consumption is no longer just a matter of cutting costs. It’s also about meeting regulatory requirements, staying competitive, and preparing for a greener maritime future.
In this post, I want to dive into three of the most impactful technical solutions for improving a ship’s energy efficiency: propeller design, hull coating, and exhaust gas cleaning systems. How do they work? What are the benefits? And where is it worth investing?
Let’s take a closer look at the innovations that are helping shipowners sail smarter.
Why Energy Efficiency Matters Now More Than Ever
Before we look at individual technologies, let’s take a moment to understand why energy efficiency is such a hot topic in shipping.
Here’s what’s driving the change:
Fuel accounts for 30–50% of a ship’s operating costs.Improving efficiency can lead to significant savings—especially as fuel prices fluctuate.
New IMO regulations (like EEXI and CII) require vessels to meet minimum efficiency levels.Ships that don’t comply may face restrictions or reduced marketability.
Environmental pressure from charterers and cargo owners is increasing.More and more stakeholders want cleaner transport solutions.
In other words: energy efficiency is not just a nice-to-have—it’s a competitive advantage.
Propeller Design: The Hidden Power of Hydrodynamics
Let’s start where the power meets the water.
How Propeller Design Affects Efficiency
The propeller might look simple, but it’s one of the most critical components for fuel efficiency. A well-designed propeller can reduce fuel consumption by 5–10% or more.
Here’s how:
Optimized blade shapes reduce resistance and improve thrust.
Variable pitch propellers adapt to different loads and speeds, increasing flexibility.
Ducted or nozzle-enhanced propellers improve flow in specific conditions (common in tugs and low-speed ships).
Even small improvements in design can lead to major cost savings over time.
New Technologies in Propeller Optimization
Computational Fluid Dynamics (CFD) simulations now allow engineers to tailor propeller designs to each vessel’s hull form and operating profile.
Tip fin technology (like Becker’s Mewis Duct or Wärtsilä’s EnergoProFin) reduces vortex losses at the blade tips.
Air lubrication systems can work in tandem with propeller upgrades to further lower drag.
✅ Real-World Example: A major container carrier upgraded its fleet with CFD-optimized propellers and energy-saving ducts. The result? An average fuel reduction of 7% per vessel, with payback in under 2 years.
Hull Coating: Smoother Surfaces, Lower Drag
What lies beneath your ship’s paint job matters more than you might think.
How Hull Condition Impacts Fuel Consumption
As a ship moves through the water, it faces hydrodynamic resistance. Over time, biofouling (like algae, barnacles, and slime) builds up on the hull, increasing drag. This means the engine has to work harder—burning more fuel.
Studies show that a fouled hull can increase fuel consumption by up to 30%.
The Role of Advanced Hull Coatings
Modern hull coatings go far beyond just preventing rust. Here’s what they do:
Antifouling paints contain biocides or silicone compounds that prevent marine organisms from attaching.
Friction-reducing coatings use advanced polymers or nanotechnology to create an ultra-smooth surface.
Self-polishing coatings slowly release active compounds over time, maintaining effectiveness without manual cleaning.
✅ Real-World Example: The Japanese shipping giant NYK Line applied low-friction, eco-friendly hull coatings across several of its vessels. They reported fuel savings of 4–8%, depending on trading routes and fouling conditions.
Exhaust Gas Cleaning Systems (Scrubbers): Compliance and Efficiency
With the IMO 2020 sulfur cap, many shipowners turned to exhaust gas cleaning systems, or scrubbers, as a solution. But scrubbers do more than just remove sulfur—they can also improve energy efficiency under the right conditions.
How Scrubbers Work
Scrubbers clean exhaust gases before they’re released into the atmosphere. They remove:
Sulfur oxides (SOx)
Particulate matter
Some nitrogen oxides (NOx), depending on design
This allows ships to continue using high-sulfur fuel oil (HSFO), which is cheaper than compliant fuels like MGO or VLSFO.
Types of Scrubbers
Open-loop systems use seawater for cleaning and discharge.
Closed-loop systems recirculate freshwater with neutralizing agents.
Hybrid systems combine both, adapting to local regulations.
Efficiency Benefits
While scrubbers add some weight and power draw, they often allow continued use of cheaper fuel, which can offset operating costs significantly.
A vessel burning HSFO with a scrubber can save $100–$200 per ton of fuel.
In high-consumption ships like VLCCs or large container vessels, the ROI can be under 18 months.
✅ Real-World Example: A Greek shipowner retrofitted ten bulk carriers with hybrid scrubbers before 2020. By continuing to burn HSFO, they saved over $1 million per vessel annually, despite the installation costs.
Strategic Tips for Shipowners: Where to Invest First
Not every efficiency upgrade makes sense for every vessel. Here’s how to prioritize:
1. Evaluate the Operating Profile
Short-haul vessels benefit more from hull coatings and propeller tweaks.
Long-haul vessels may justify scrubbers and propulsion upgrades due to higher fuel volume.
2. Consider Retrofit Potential
Not every upgrade needs a newbuild.Many propeller and coating improvements can be added during regular dry-dock periods.
Scrubber installations are more complex, but often feasible for ships with long remaining lifespans.
3. Use Third-Party Efficiency Audits
Marine consultants can simulate savings based on your specific route, engine type, and load patterns.
These audits often cost a few thousand euros—but can unlock six-figure savings.
4. Monitor Fuel Prices and Regulatory Trends
The economics of scrubbers depend heavily on fuel price spreads.
Hull coatings and propeller upgrades are less affected by fuel type—and are more predictable in ROI.
Final Thoughts: Efficiency is the New Standard
Energy efficiency is no longer just a box to tick—it’s a strategic decision with real financial and operational consequences.
✅ Propeller design improvements can reduce resistance and enhance performance.
✅ Advanced hull coatings minimize biofouling and keep ships running smoothly.
✅ Scrubbers help meet emission rules while unlocking fuel savings.
✅ Shipowners who invest in the right upgrades today will reap the rewards tomorrow.
In a competitive and decarbonizing market, small tweaks can lead to big wins. And when you combine the right tech with smart planning, efficiency becomes more than just compliance—it becomes your edge.
Have you implemented any of these upgrades on your vessels? What results did you see? Share your stories or questions in the comments—I look forward to the exchange!

Comments